2、台液位计中伺服液位计选用高精度计量及用来做储罐计量,雷达液位计为控制及用于与高液位开关做联锁,关闭罐根阀。
从PID 图中可以看出从PID 图中可以看出虽然增加了SIS 系统,但是接入其中的信号并不多,只有一点AI、一点DI、一点DO。其余信号仍然在DCS 系统中进行检测及报警。
设计的SIS 系统具体联锁控制如下:当储罐的液位计或液位开关任一液位高于设定值时,SIS 系统进行联锁,关闭储罐罐根切断阀,防止储罐罐液位继续升高,引发冒罐危险[1] 。
4、SIS 系统设计
4.1 SIS 系统的设置原则
罐区SIS 系统,作为全厂SIS 系统的组成部分,根据装置的特点,实现罐区内重要的安全联锁保护、紧急停车系统及关键设备联锁保护。SIS 系统设置在现场机柜室,设置独立的控制器,以确保人员及生产装置、重要机组和关键设备的安全。SIS 系统的安全综合等级根据相应的要求进行考虑。SIS 系统按照DIN V VDE0801 和DIN V 19250 标准,采用TüV 或AK6 安全认证的SIL3 级的安全可编程序控制器(Programmable Logic Controller - PLC) 完成装置的紧急停车(EmergencyShut-Down - ESD) 和紧急泄压(EmergencyDepression - EDP)。SIS 系统按照故障安全型设计,与DCS系统实时数据通讯。SIS 系统设工程师站,SOE 站,相应的报警及操作通过辅助操作台上开关、按钮、声光报警装置和DCS 系统的操作站来完成。罐区SIS 系统具有报警事件顺序记录功能(SOE),在中央控制室和现场机柜室各设置一套工程师站,用于SIS 系统的组态、下装、调试和日常维护以及报警事件顺序的记录。中央逻辑控制器、输入/ 输出卡件、SIS 系统内部的安全网络、供电单元、与DCS 系统通信的单元均采用冗余结构。SIS 系统应配有HART 信息采集器,用于采集现场智能仪表HART 信息,并通讯至AMS 系统。SIS 与DCS 通信卡必须是冗余配置, 且冗余的两个通信接口不应在同一块通信卡上。冗余数据通信系统应能够自动切换,并可进行系统诊断报警。在切换时不允许有数据丢失。通信系统为控制站与控制站之间、控制器与工程师站/SOE 工作站提供可靠的高速数据传输。传输速率不小于100Mbps。SIS 系统支持标准通信协议,冗余容错串行通信方式。SIS 与DCS 通信协议为MODBUS RTU 或TCP/IP。DCS 系统为主站,SIS 系统为从站。所有部件都应抗每米10 毫伏场强的电磁及无线电干扰。SIS 系统具有时钟同步的性能, SIS 系统控制器的时钟在系统上电和更换时钟卡件后,能够自动进行同步。SIS 系统时钟同步信号来自于DCS 系统。
根据《石油化工仪表系统防雷工程设计规范》进行仪表系统防雷工程设计。SIL3 回路的现场仪表侧及控制室(现场机柜室)侧配置防雷电浪涌保护器。
在工厂调试完成后,有20% 已经接好线的输入/ 输出(I/O) 点作为备用;在端子接线柜中,有20% 的裕量端子作为备用;在系统机柜中,有20% 的裕量空间用于安装I/O 卡件。
在工厂调试完成后,处理器、数据存贮器和数据通信网络的负载最高不超过40%;电源单元的负载最多达到其能力的50%;应用软件和通信系统有30% 的扩展能力。
4.2 SIS 系统网络结构
本项目采用冗余、容错结构的故障安全型SIS 系统,安全等级达到SIL3。
根据图2 罐区网络结构图,可见:罐区单元主要硬件设备为:1 台系统柜、3 台辅助柜(端子柜、继电器柜、安全栅柜)、2 台SOE 工程师站、2 台交换机、1 台打印机。
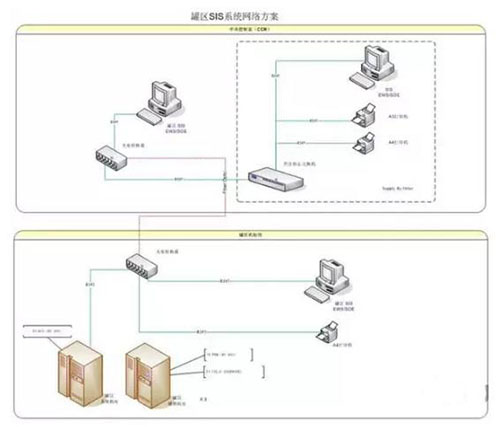
1) 软件组态:编程语言应符合IEEC 61131-3 工业标准。
2) 软件组态的安全性:采用PROM 或EPROM 存储器存储应用软件,提供防止未被授权人员修改程序的功能。软件应能在线修改及下装。
3) 编程软件:工程师站用于修改控制程序,诊断显示,离线/ 在线程序调试和现场装置的维护。系统软件包括系统诊断,工程,监视和删除故障功能。
4) 系统应提供重要的时序事件记录(SOE)和过程历史报告。
5、结束语
由于石油化工重大危险源本身存在的巨大危害性及其可能造成二次危害的特性,对于石油化工重大危险源的安全控制工作至关重要。对于储存大量易燃易爆、可燃有毒介质的化工项目,构成重大危险源的储罐区采用安全仪表系统(SIS)进行安全监控及联锁控制系统的设计是符合时代发展趋势的。