间冷燃气轮机循环系统,通过间冷器大幅降低进入高压压气机气流的温度,减少高压压气机的压缩耗功,从而提高燃机的输出功率,是燃机发展的重要方向。间冷器作为间冷循环燃机系统的关键设备,其技术难点在于:换热器流道结构复杂,缺乏成熟设计方法;对换热效率和紧凑度要求极高,同时又要求阻力损失极低;对换热器加工工艺精确度和可靠性要求高。特别是对体积、重量、热负荷、功耗、耐蚀性等有苛刻要求的间冷燃机系统,间冷器一直是多年来难以克服的技术瓶颈,制约着我国先进燃机系统的发展和应用。
中科院工程热物理所传热中心在研究所创新引导基金项目“燃机新型高效紧凑式间冷器研发”的支持下,开展了大中型燃机间冷器高效低阻传热机理、结构完整性设计、高精度加工和宽板幅焊接等关键技术攻关,先后取得了一系列重要成果。针对大中型燃机对间冷器高效、低阻、高紧凑性的要求,基于传热强化理论的最新成果结合研究团队提出的“耦合分布、协同优化”的换热器设计思想,发展了新型气液两则流道局部和结构形式。
基于多目标多参数协同优化思想,在体积、重量、压损等严格限制条件下,寻求综合换热性能最优的板厚、肋高、通道宽和通道数量等多个设计参数间的最佳组合,从而获得Pareto最优设计方案。针对微小通道换热器复杂结构形式和通道布局,基于多尺度耦合模拟技术结合周期性条件开展了大规模跨尺度高精度数值仿真研究,用于指导新型换热结构的开发和优化定型;针对大宽幅大流量下流量分布不均的问题,基于热质传递理论开展入口区域流量分布均匀性研究,提出了多边形换热结构流体入口区域通道分布新形式,有效提高了流量分布的均匀性。由于恶劣工作环境以及燃机启停等运行条件,使间冷器常处于非满负荷设计工况条件下运行,研究团体建立了多变量非线性间冷模块动态优化模型,用于研究各种恶劣条件非设计工况下间冷器性能及对燃机系统的影响。研究团队先后多次在研究所廊坊研发中心开展了全温全压间冷器实验缩比样机的测试验证,并邀请有关专家领导到测试现场指导和审核,测试结果显示样机冷热流体两侧的换热性能、压力损失等各项指标均优于原设计目标和实际要求。测试结果和设计计算结果以及仿真结果对比显示,热负荷平均误差在2%以内,宽板幅出口截面温度和压力不均匀度小于1.5%,证实了研究团队开发的换热器设计方法和大规模跨尺度数值仿真技术的准确性和可靠性。
研究团队基于“通道-芯体-整体”的由局部到整体换热器设计思路,通过对实验样机的优化改进和放大,结合当前加工焊接等工艺,完成了新型高效全尺寸原型机的设计、加工和制造,突破了宽幅板材流道设计、结构优化、精密加工、无钎料焊接等关键技术,能够满足恶劣工作环境下高强度、耐腐蚀等严酷要求。近日,研究所加工的新型高效全尺寸间冷器原型机在相关单位测试平台完成了全温全压全工况下性能测试,各项指标均达到或优于原设计和实际要求,与现有间冷器产品相比在综合性能和加工工艺等方面均具有明显的技术优势,并得到有关单位领导专家的高度认可。
间冷系统能够有效提高燃机效率、降低燃油消耗,在间冷燃机系统中起关键作用,具有广阔的应用前景。相比世界先进的间冷燃机技术,国内燃机技术水平尚有一定差距,其中间冷器正是制约间冷燃机系统发展的关键技术瓶颈之一。中科院工程热物理所传热中心间冷器研发团队,经过一年半的技术攻关,克服了通道形式、结构设计、芯体优化、整体成型等一系列从设计到优化、从理论到工艺的技术难关,形成了具有自主知识产权的新型高效低阻紧凑式间冷器设计方法和优化思想,并在通道布局、结构创新、加工焊接工艺等方面形成了多项国家发明专利。中科院工程热物理所全温全压全尺寸新型高效间冷模块的研发成功,将我国大中型燃气轮机中间冷却技术提升到一个新的高度,填补了国内相关技术空白,有助于我国先进燃机技术早日赶超世界先进水平。
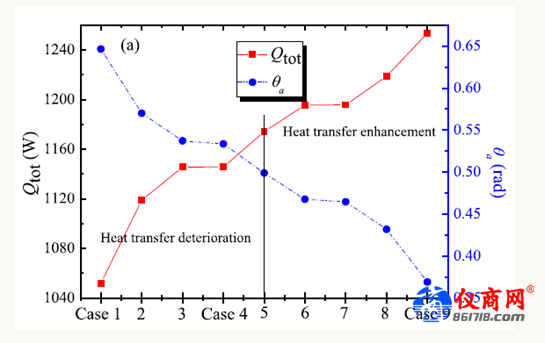
图2 新型换热通道结构传热机理分析(崔欣莹,郭江峰等, 《Int. J. Heat Mass Transfer》, 2018)