随着社会的发展,钢管的需求量越来越大,尤其是一些广泛应用于航空、军工、原子能与空间技术等领域的高精度、薄壁、高强度钢管的需求量逐步增加。钢管生产中存在的缺陷,以及这些缺陷潜在的危害已成为大家关注的焦点。本文结合理论分析和实际检测实验,探讨了超声波探伤技术在薄壁小管径钢管分层自动检测应用中的可行性。实验结果表明,利用超声波探伤仪,可实现薄壁小管径钢管分层自动检测。
1.水浸法超声波检测原理
小口径、薄壁钢管由于曲率大、管壁薄,在自动化检测中采用直接接触法检测难以实现,故一般采用水浸法超声波检测。其检测原理是:将水浸超声波纵波聚焦探头置于水中。利用超声波纵波聚焦探头发出的超声纵波垂直入射到钢管管壁中,当声波遇到管壁中的分层缺陷时,产生反射回波,反射波沿原路返回被探头接收。如图1所示。
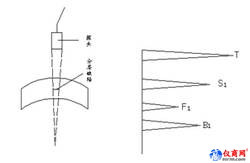
图1 水浸法超声波检测分层原理图
2.检测参数的选择
在实际检测中,由于声波是垂直入射到钢管表面,因此钢与水的界面回波很强,造成回波中界面波很宽,检测盲区大。尤其是在检测薄壁管时,界面波甚至覆盖一次底面回波,使分层检测无法实施。为解决这个问题,需调整检测参数,提高检测的分辨率。在水浸法超声波检测中,与检测分辨率相关的参数有:探头参数(包括频率、晶片尺寸、聚焦探头的焦距)、仪器参数(包括脉冲宽度、检波方式、匹配等)。
2.1 探头参数的选择
2.1.1探头频率 超声波纵波可检出的最小缺陷尺寸与探头频率有关,即频率越高,检测的灵敏度和分辨率越高。为提高检测的分辨率应尽量选择高频探头,但频率越高,声波在水中的衰减也越大,这又直接影响到了超声波的回波幅度,不利于检测灵敏度的提高。综合考虑,探头频率选在5~10 MHz较为合适。
2.1.2探头的晶片尺寸 晶片尺寸越大,声波的指向性越好,但检测的分辨率越差。同时晶片尺寸的大小也与检测效率有关,即探头的有效检测区域越大,则检测效率越高。在自动化检测分层时,为了不漏检,通常选用的线聚焦探头轴线晶片尺寸为被检测平底孔直径的2倍。对于点聚焦探头,其情况视其要求的有效检测区域而定。
2.1.3聚焦探头的焦距 在小口径钢管检测中,为保证声束两侧的一致性,通常探头水中焦点与钢管的圆心重合,即F=H+R,F为探头水中焦距,H为水层厚度,R为钢管半径。其中H作为中间耦合剂的水层厚度在纵波检测中应使水、钢的二次界面波S2出现在底波B1之后。同时H还应小于声场的近场区N,以避免声束在入射面发生大量的散射而使探伤灵敏度降低,即N>H>(VL1/VL2)T。VL1=1450 m/s为水中纵波声速,VL2=5850 m/s为钢中纵波声速。在这里需要指出的是对于一些薄壁管的分层检测,当钢/水一次界面波S1与底波B1无法分开时,适当调整水层厚度,可选用2~3次伤波探伤,特别是对于据与管壁中间的分层,由于声波的干涉效应,3~4次分层回波最高,探伤效果最佳。如图2所示。
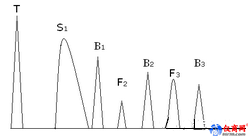